Maximizing Efficiency: Strategies for Operating Aggregate Crushers
- sophieaimix
- Feb 20, 2024
- 3 min read
Aggregate crushers play a crucial role in the construction industry by transforming large rocks into smaller, more manageable pieces that can be used in various construction projects. To ensure optimal productivity and cost-effectiveness, it is essential to implement strategies for operating aggregate crushers efficiently. In this article, we explore key strategies to maximize the efficiency of aggregate crushers.
Regular Maintenance and Inspection
Regular maintenance and inspection are paramount for optimizing the efficiency of aggregate crushers. Establishing a proactive maintenance schedule and conducting routine inspections help identify potential issues early and prevent costly breakdowns. Maintenance tasks such as lubricating moving parts, checking wear components, and inspecting electrical
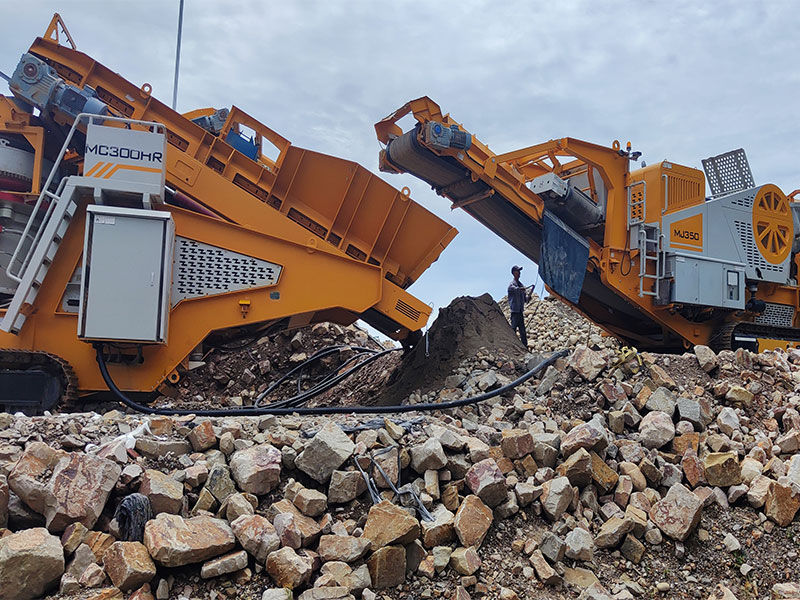
systems should be performed regularly to ensure smooth operation and minimize downtime.
Operator Training and Skill Development
Investing in operator training and skill development is crucial for maximizing the efficiency of aggregate crushers. Well-trained operators possess the knowledge and expertise to operate the crushers effectively, troubleshoot common issues, and adhere to safety protocols. Providing comprehensive training programs on crusher operation, maintenance procedures, and safety guidelines empowers operators to maximize crusher performance, minimize errors, and ensure safe operation.
Optimal Feed Material Management
Managing the feed material effectively is essential for maximizing the efficiency of aggregate crushers. Proper feed material selection, sizing, and distribution ensure consistent and uniform feeding to the crusher, minimizing variations in feed size and maximizing crusher throughput. Implementing measures to control the feed material flow rate and remove oversized or contaminated materials before they reach the crusher helps prevent blockages, reduce wear on crusher components, and improve overall efficiency.
Adjusting Crusher Parameters
Adjusting crusher parameters according to the characteristics of the feed material and desired end-product specifications is critical for optimizing crusher efficiency. Parameters such as crusher speed, closed-side setting (CSS), and crusher chamber configuration can significantly impact crusher performance and product quality. Regularly monitoring and adjusting these parameters based on operating conditions and production requirements ensure optimal crusher performance and efficiency.
Utilizing Automation and Technology
Embracing automation and technology can significantly enhance the efficiency of mobile jaw crushing plant. Modern crushers are equipped with advanced features such as automated controls, remote monitoring systems, and predictive maintenance capabilities. Leveraging these technologies allows operators to monitor crusher performance in real-time, adjust settings remotely, and identify potential issues before they escalate. Additionally, incorporating automation streamlines crusher operations, reduces operator workload, and improves overall efficiency.

Proper Crusher Selection and Configuration
Selecting the appropriate crusher type and configuration for specific application requirements is essential for maximizing efficiency. Consider factors such as feed material characteristics, desired product specifications, and production capacity when choosing a crusher. Whether using a jaw crusher, cone crusher, impact crusher, or gyratory crusher, selecting the right size and configuration ensures optimal performance and efficiency in crushing operations.
Monitoring and Optimization
Continuous monitoring and optimization of crusher performance are essential for maintaining peak efficiency levels. Monitoring key performance indicators such as crusher throughput, power consumption, and product quality enable operators to identify trends, diagnose inefficiencies, and implement corrective actions. Regularly analyzing operational data and performance metrics helps optimize crusher settings, improve efficiency, and minimize operating costs over time.
Conclusion
In conclusion, maximizing the efficiency of aggregate crushers requires a multifaceted approach that encompasses regular maintenance and inspection, operator training and skill development, optimal feed material management, adjusting crusher parameters, utilizing automation and technology, proper crusher selection and configuration, and continuous monitoring and optimization. By implementing these strategies, operators can enhance crusher performance, minimize downtime, and improve overall productivity and cost-effectiveness in aggregate crushing operations. Investing in efficient crusher operation contributes to the success of construction projects, ensures timely delivery of high-quality aggregates, and ultimately enhances customer satisfaction in the construction industry.
Comments